Dismayed by the ever-expanding plastic pollution clogging up our oceans and killing our sea life, oceanographer Julie Reisser has formulated a climate-positive way to replace plastic altogether (and it shares some similarities with beer)
For many years, marine scientist Julia Reisser devoted her life to finding ways to clean up plastic pollution in our oceans. It was after tracking local sea turtles and a doctorate on plastic pollution through the University of Western Australia that the Perth-based Brazilian had an epiphany.
Why not use seaweed – one of the good news stories from our oceans given their high carbon dioxide removal rates and quick growth – to create a new material that replicated plastic, was climate positive and could ultimately eradicate plastic altogether?
When Julia was introduced to Michael Kingsbury, a former business executive and M&A lawyer with a focus on science-driven businesses, the pair decided to dedicate themselves to doing just that. In 2020 they co-founded climate tech company Uluu.
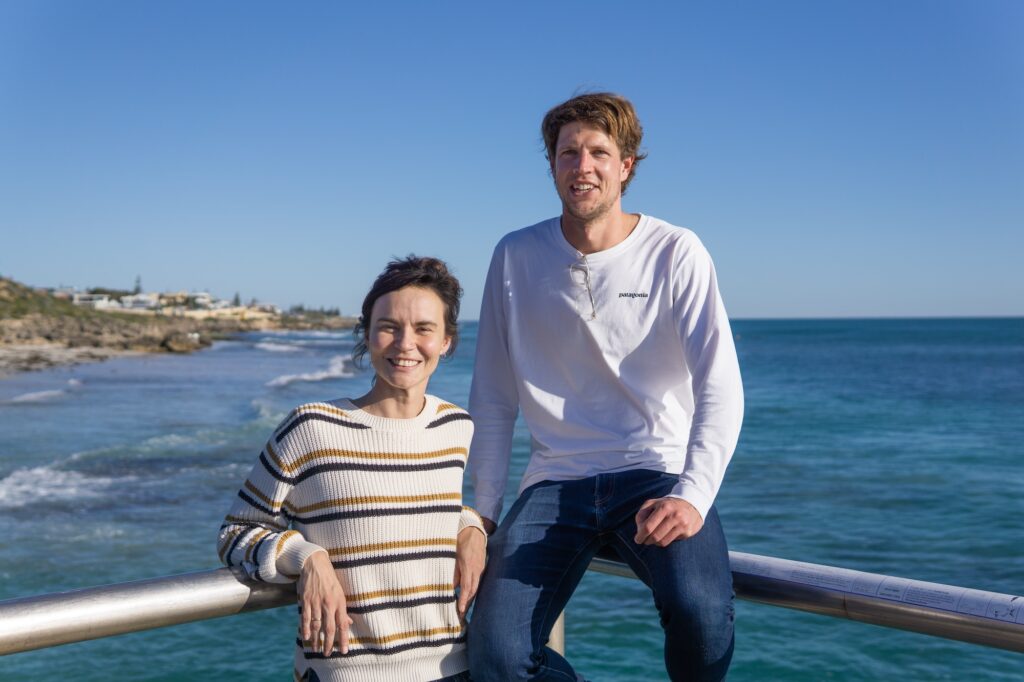
Uluu founders Dr Julia Reisser and Michael Kingsbury
Alberts Impact Ventures was one of the first to commit early-stage funding, alongside the CSIRO’s VC fund Main Sequence.
“We look to work with pioneering founders with a pioneering vision and that is exactly what we’ve found with Uluu. An amazing team with a vision to have a significant impact on multiple issues facing our planet,” says Alberts head of impact Emily Albert, noting Uluu addressed two of Alberts impact focus areas: equality and a sustainable environment.
“Uluu will not only tackle plastic pollution and decouple our polymer economy from fossil fuels but, in sequestering carbon, has the potential to benefit the world.”
Uluu hasn’t looked back, and today has grown to a 14-strong team including international seaweed biotechnology scientists and engineers working out of Uluu’s seafront labs in Perth’s Indian Ocean Marine Research Centre.
To land on the perfect seaweed, Uluu tested 35 different types, ultimately choosing Gracilaria, a variety that grows all over the world but is already being farmed in Indonesia for agar, meaning Uluu could tap into an existing market and buy the feedstock at scale.
The process of manufacturing Uluu – also the product name – involves cooking the seaweed in large vats of seawater using enzymes to extract the sugars. The sugary liquid is then fermented with microorganisms, a process not dissimilar to brewing beer. The fermentation process produces a type of PHA (polyhydroxyalkanoate), a natural polymer that ultimately mimics the properties of plastic but is biodegradable and carbon negative. The process uses seawater rather than freshwater, a natural steriliser that also eliminates the need for harmful chemicals or solvents.
The leftover biomass, a solid protein-rich byproduct can be used for fish feed or potentially refined for human consumption, providing an additional revenue stream.
The PHA pellets can then be compounded into other products usually made from plastic, from cosmetics packaging to furniture and textiles. In January, Uluu announced a partnership with surf brand Quicksilver, producing a surf wax comb that replaces the need for rigid plastics.
“There are three areas we’re looking to tackle: plastic pollution, climate change and ocean health,” says Uluu’s communications and sustainability lead, Michelle Wheeler. While currently very little plastic is properly recycled, often ending up as landfill, polluting our oceans or being burnt, Uluu is biodegradable and home compostable. Uluu is also climate positive given seaweed absorbs carbon as it grows; while farmed seaweed provides additional bioremediation benefits addressing fertiliser run-off and excess nitrogen in the water while providing jobs for local coastal communities.
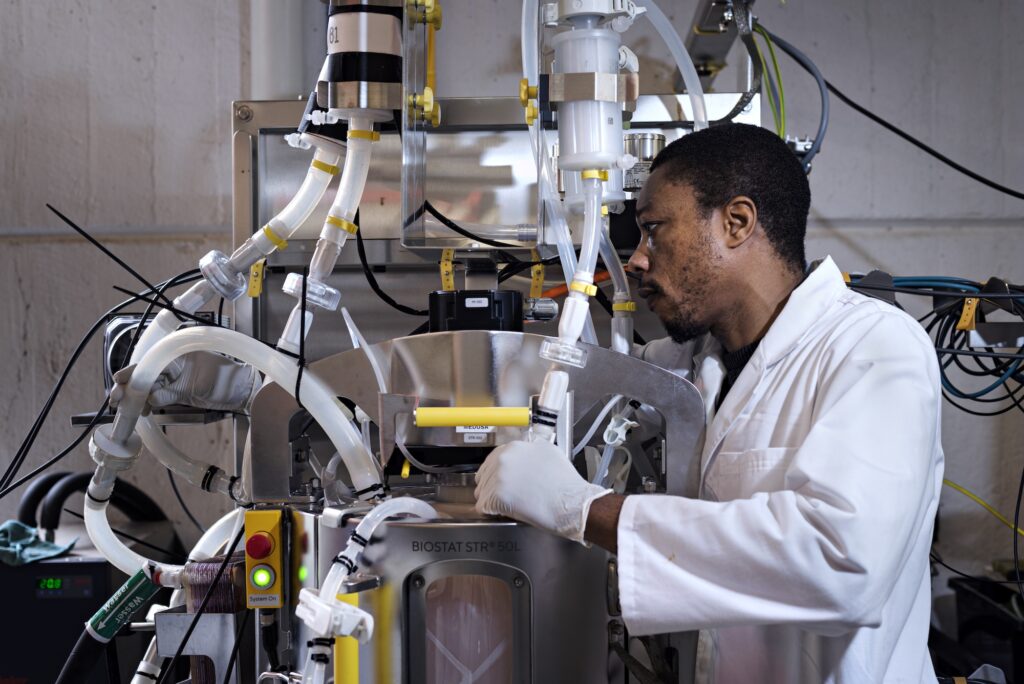
Uluu production lead Dr David Chuka Ogwude checks on a fermenter.
Uluu continues to kick goals. In 2022, the company was named the inaugural winner of the $100,000 KPMG Nature Positive prize, a resounding endorsement of the founders’ vision to replace plastics with climate-positive materials with the additional benefit of pro-bono advisory support.
In June, Uluu received a $200,000 grant from the West Australian government that will be used to purchase semi-industrial manufacturing equipment for their lab, increasing their ability to further manufacture prototypes in-house.
“We have amazing scientists and engineers who are always looking to refine the process along the whole chain from extracting seaweed sugars to fermentation and manufacturing,” says Michelle. “We only produce relatively small quantities at the moment, around 1-2kg a week. It’s enough to do small production runs and customer trials [but] we’d love to start making more.”
With around 10kg of seaweed needed to make 1kg of plastic alternative, Uluu is also researching Australian varieties of seaweed so they can farm it locally, bringing the farming and manufacturing together.
The company is now focussed on moving into textiles and is collaborating with Deakin University to research the process and develop the first prototype to see how the fabric feels and performs.
“We’re really excited about the emerging area of textiles where we can produce fabric that replaces polyesters, fabric that could be waterproof and produce clothing like activewear that is biodegradable but without the microplastics when you wash it,” says Michelle. “It’s been great collaborating with Deakin University to develop the first prototype and get a feel for the fabric and how it performs.”
The other big focus for Uluu now is cosmetics packaging, and the company is working with a couple of brands to test Uluu’s compatibility with their formulations.
Adds Michelle, “We can’t wait to create a plastic-free future.”